
شرح فرآنتد تولید بر اساس OPC خط
فسفاته و صابونی
هدف اصلی قسمت فسفاته کردن ایجاد پوشش تبدیلی ورق فقط فولادی جهت کشش سرد است که شامل 9 مرحله ذیل می باشد:
1. وان چربی گیری :
ورق های فولادی به تعداد 15 عدد داخل سبد قرار گرفته و به مدت 10 دقیقه داخل وان چربی گیری که محتوی یک نوع دترژنت (ماده شوینده)است، می شود و عملیات چربی زدایی در حین این مدت انجام می شود.
2. وان آب شویی :
ورق های فولادی چربی گیری شده به مدت یک دقیقه شستشو داده می شود.
3. وان زنگ بری:
سبد حاوی 15 ورق فولادی جهت حذف اکسید آهن از سطح ورق داخل وان زنگ بری می شود.
4. وان آب شویی :
ورق های فولادی زنگ بری شده جهت حذف خاصیت اسیدی سطح ورق ها ، وارد وان آب شویی می شود.
5. وان آب شویی :
جهت زدودن کامل خاصیت اسیدی ، ورق های فولادی برای بار دوم وارد وان آب شویی می شوند.
6. وان فسفاته :
ورق های فولادی به مدت 10 دقیقه داخل محلول فسفات تریکاتیونیک به صورت غوطه ور قرار می گیرد تا یک پوشش تبدیلی برای ورق فولادی ایجاد گردد.
7. وان آب شویی :
جهت حذف خاصیت اسید ی از سطح ورق های فولادی ، آب شویی در این مرحله انجام می شود.
8. وان صابونی کردن :
هدف از این عمل کاهش اصطکاک دستگاه پرس با ورق فولادی می باشد. ورق های فولادی به صورت غوطه وری داخل وان صابونی به مدت 10 دقیقه قرار می گیرند.
9. مرحله خشک کردن :
در این مرحله ، صابونی که در مرحله قبل روی سطح ورق ها نشسته ، خشک می شود و ورق فولادی پوشیده از صابون آماده تحویل به تولید می شود.
لازم به ذکر است قبل از انجام مرحله فسفاته و صابونی تست مواد اولیه به شرح ذیل انجام می شود:
هدف از انجام فرایند تست مواد ورودی ، تطبیق مشخصات ورق فولادی مورد استفاده با ورق مورد نیاز شرکت می باشد.
مواد اولیه
ورق فولادی : نوع ورق CR34M04 با ضخامت 12میلیمتر
کاپ فولادی : نوع ورق CR34M04 با ضخامت حداقل 8.2 میلیمتر
نوع آلیاژ مواد اولیه
پرس های گرم
وظیفه خط پرس ، فرم دهی ورق جهت تولید کاپ می باشد.
پرسهای خط تولید مخزن ، شامل 3 پرس هیدرولیک که دارای مشخصات ذیل می باشد:
پرس اول: تناژ این پرس 2000تن با کورس 1.6 متر می باشد.
پرس دوم: تناژ این پرس 1200 تن با کورس 2.20 متر می باشد.
پرس سوم: تناژ این پرس 1200 تن با کورس 2.20 متر می باشد.
در پرس مرحله اول کاپ خروجی از پرس سرد ، بعد از گرم شدن در کوره القایی به صورت گرم کشیده می شود. قالب این مرحله شامل یک دست سنبه و ماتریس به همراه اجکتور می باشد که جنس سنبه و ماتریس از فولاد گرم کار و جنس اجکتور از فولاد معمولی می باشد.
در این مرحله کاپ به طول 60 سانتی متر با قطر 42 سانتی متر به ضخامت 12 میلی متر تبدیل می گردد.
در پرس مرحله دوم ، کاپ خروجی مرحله قبل بعد از گرم شدن در کوره القایی به صورت گرم کشیده می شود. قالب این مرحله شامل یک دست سنبه و ماتریس به همراه اجکتور می باشد که جنس سنبه و ماتریس از فولاد گرم کار و جنس اجکتور از فولاد معمولی می باشد.
در این مرحله کاپ به طول 850 سانتی متر با قطر 356 سانتی متر تبدیل می گردد.
وظیفه پرس آخر عمل سایزینگ می باشد که کاپ بدست آمده از مرحله سوم را به اندازه نهایی دلخواه می رساند. این قالب نیز شامل یک دست سنبه و ماتریس فولادی می باشد .
در این مرحله کاپ به طول 90 سانتی متر با قطر 356 میلی متر و به ضخامت 8 میلی متر تبدیل می گردد.
دستگاه هات اسپینینگ
هات اسپینینگ فرایندی است که در آن شکل دهی لوله در حال دوران با دور مناسب و به وسیله غلطک فرم دهی انجام می شود.
به وسیله فرایند فوق می توان عملیات Necking(شکل دادن گلویی سیلندر) و Bottom Closing (بستن انتهای لوله) را انجام داد.
در آغاز فرایند ، مرحله پیش گرمایش بوسیله کوره القایی انجام میشود و دمای لوله به حدود 1100-1000 درجه سانتیگراد رسانده می شود و در گام بعدی لوله به وسیله Spindle (محور دورانی) تا حدود 500 دور در دقیقه چرخانده شده و عملیات فرم دهی گرم بوسیله غلظت فرم دهی آغاز می شود.
از آنجا که افت دمای لوله در حین فرایند مجاز نیست ، دو مشعل که با گاز و اکسیژن کار می کنند وظیفه تثبیت دما را بر عهده دارند و هنگامی که غلطک ، فرم دهی را انجام می دهد ، مشعلهای فوق الذکر روشن شده که با حرارت و شعله ایجاد شده اجازه نمی دهند دمای لوله پایین تر از 1000 درجه سانتیگراد برسد.
کوره هاردنینگ
هدف از انجام این فرایند افزایش سطح سختی مخزن می باشد.
در این مرحله مخزن در دمای بالایی در زمان تعیین شده (یک ساعت) مرحله به مرحله گرم شده تا به دمای نهایی 890 درجه سانتیگراد برسد. در این مرحله به مخزن حرارت بسیار بالایی وارد می شود.این کوره شامل 12 مشعل است و گنجایش 26 عدد مخزن را دارا می باشد.
مخزن بعد از خروج از کوره باید بلافاصله وارد مایع کوئنچ شود . در این قسمت زمان خیلی مهم است. مخزنی که بلافاصله بعد از خروج از کوره وارد مایع کوئنچ نشود ارجاعی محسوب می شود.
وان کوئنچینگ
هدف از انجام این فرایند افزایش سطح سختی مخزن می باشد.
مخزن بعد از خروج از کوره Hardening باید بلافاصله وارد مایع کوئنچ شود.
در این قسمت زمان خیلی مهم است.
مخزنی که بلافاصله بعد از خروج از کوره وارد مایع کوئنچ نشود ارجاعی محسوب می شود.
در مرحله مایع کوئنچ ، با وارد کردن شوک ناگهانی به مخزن در عرض 30 ثانیه ، دمای بالای آن گرفته شده و به دمای محیط برمی گردد.
عواملی از قبیل جنس مایع کوئنچ، زمان ماندگاری در کوئنچ، دمای مایع کوئنچ در ایجاد سختی مخزن تاثیر بسزایی دارند.
گوره تمپرینگ
هدف از انجام این فرایند افزایش سطح سختی مخزن می باشد.
در مرحله Hardening ، حرارت بالایی به مخزن وارد شده و بلافاصله با ورود به مایع کوئنچ باعث شکل گرفتن سریع مولکولهای مخزن و سختی بالای آن شده ، و این سختی بسیار بالا است و نیاز به سختی کمتر از این می باشد. بنابراین در مرحله Tempering مخزن دوباره بازپخت شده تا به سختی مورد نظر تعیین شده برسد.
در این مرحله دمای مخزن به دمای نهایی 630 درجه سانتیگراد می رسد.
الواتورخنک کننده مخزن
هدف از انجام این فرایند خنک کردن مخازن جهت انجام تست ها می باشد.
مخزن CNG بعد از اینکه از کوره عملیات حرارتی خارج شد باید در مرحله تست و آزمایش قرار گیرد ولی به علت درجه حرارت بالایی که دارد این عمل امکان پذیر نمی باشد. در این حالت ابتدا باید مخزن CNG خنک و سرد شود تا به مرحله تست برسد.
جهت خنک کردن مخازن CNG :
مخزن ها داخل حلقه های الواتر قرار می گیرند و با چرخش دورانی الواتور و با استفاده از فن های الکتریکی به صورت پیوسته و با سرعت مشخص سرد می شوند تا از سخت شدن مجدد مخزن جلوگیری به عمل آید.
تست سختی سنجی
طبق بند 33-8 آزمون سختي سنجي بايد براساس استاندارد ملي ايران ، بر روي ماده بخش استوانهاي مركزي و بخش انتهايي عدسي مربوط به هر مخزن يا لايه داخلي انجام گيرد. اين آزمون بايد بعد از عمليات حرارتي نهايي انجام گيرد.
مقادير سختي كه در اين آزمون بدست ميآيد بايد در محدوده مشخص شده طراحي باشد.
دستگاه شات بلاست خارجی
هدف از انجام این فرایند ، شستشو و اکسید زدایی سطح خارجی مخزن CNG توسط ساچمه می باشد.
مخزن ها پس از وارد شدن در داخل دستگاه ، توسط حرکت چرخشی جلو برنده به سمت اتاقک حمله رفته و توسط دو عدد توربین ، ساچمه ها بر روی سطح قطعه پاشیده می شود و شستشوی سطحی جهت زدودن اکسید انجام می شود. کل این فرایند 6 دقیقه طول می کشد.
شات بلاست خارج در کل فرایند تولید مخزن ، دو بار انجام می شود یکبار بعد از سختی سنجی و یکبار قبل از فرایند رنگ.
دستگاه حکاکی
هدف از انجام این فرایند حکاکی مشخصات مخزن بر روی آن می باشد.
این دستگاه شامل فیکسچر ، سیستم کنترل نرم افزاری و هد حکاکی بوده و توسط فشار باد مشخصات مخزن را بر روی مخزن حک می کند.
مشخصات حکاکی شده بر روی مخزن کاملا مطابق استاندارد ECE R110 می باشد.
ماشین تراش 36 ابزاره
هدف از انجام این مرحله ماشین کاری قسمت گلویی مخزن می باشد.
مخزنها پس از قرار گرفتن در قسمت فیکسچر در داخل دستگاه اره نواری گلویی ، توسط حرکت عمودی اره ، در سایز مورد نظر بریده می شوند.
جهت خنک کردن گلویی در حال برش از پاشش آب و صابون بر روی دستگاه استفاده می شود سپس مخزن ها پس از قرار گرفتن در قسمت فیکسچر مربوطه به داخل دستگاه هدایت شده و توسط 4 ابزار عملیات سوراخ کاری ، روتراشی ، دیواره تراشی ، پله زنی و قلاویز کاری صورت می گیرد.
روتراشی و رزوه کاری سر گلویی مخزن نیز توسط این قسمت انجام می شود.
جهت خنک کردن گلویی ، از پاشش آب و صابون توسط نازل بر روی دستگاه استفاده می شود.
لازم به ذکر است که دقت دستگاه در حد صدم میلیمتر است.
تست هیدرو استاتیک
در اين آزمون ، فشار هيدرواستاتيك مخزن بايد بتدريج و بطور منظم افزايش يابد تا اينكه فشار ، به حداقل 5/1 برابر فشار كاري برسد.
به منظور حصول اطمينان از عدم ايجاد نشتي و اينكه فشار رو به كاهش نميباشد، مدت زمان اعمال فشار آزمون بايد حداقل 30 ثانيه باشد.
شات بلاست داخلی
هدف از انجام این مرحله شستشو و اکسید زدایی سطح داخل مخزن توسط ساچمه می باشد.
این دستگاه قابلیت شات بلاست دو مخزن به طور همزمان را دارا می باشد. شامل سیستم پاشش ساچمه توسط مخزن ، دیگ ساچمه ، کمپرسور هوا و نازل پاشش می باشد.
در این مرحله ساچمه توسط نازل به داخل مخزن پاشیده می شود.
کیفیت سطح بدست آمده در حد SA2.5 می باشد.
بازرسی چشمی
سطوح داخلی و خارجی تمامی مخازن باید جهت شناسایی عیوب ظاهری مثل برآمدگی ، فرورفتگی ، کندگی ، ترک ، روی هم افتادگی و سایر عیوب تعیین شده در استاندارد ، مورد بازرسی قرار بگیرد.

۱۲ عادت جالب بیزینسمنها که آنها را از بقیه متمایز میکند
12 عادت جالب بیزینسمنها که آنها را از بقیه متمایز میکند
چه چیزی بیزینسمنهای موفق را از سایرین متمایز میکند؟ این افراد چه عادتهایی دارند که دیگران توجهی به آنها نمیکنند؟
توسط حمید محمودزاده –
به روزرسانی شده در ۲ آذر ۱۴۰۰ –
زمان مطالعه 5 دقیقه
چه چیزی یک بیزینسمن را از بقیه متمایز میکند؟ حتما میدانید که چیزی باعث برتری و موفقیت این افراد میشود! اما کلید موفقیت این افراد چیست؟ چگونه باید شبیه رهبران بزرگی مانند ایلان ماسک و جف بزوس رفتار و فکر کنیم؟ همه ما دوست داریم مثل یک بیزینسمن ثروتمند و معروف باشیم. به همین دلیل ما هم به سراغ مطالعه و بررسی این موضوع رفتیم. موارد زیر، عادتها و رفتارهای متداولی است که اکثر بیزینسمنها دارند. جالب است بدانید همین عادتها – که شاید به نظرتان کوچک یا بیاهمیت باشند – افراد موفق را از عامهی مردم متمایز میکنند.
۱. مدیریت زمان
همه دوست دارند که برنامه مشخصی برای اهداف و زندگیشان داشته باشند. احتمالا شما هم حداقل یک بار به سراغ برنامهریزی کوتاه مدت و بلندمدت رفته باشید؛ و احتمالا بدانید که این برنامهریزیها در ۹۰ درصد موارد به شکست کامل میرسند. مهمترین دلیل هم بلندپروازی بیش از حد و اشتباه تخمین زدن مدت زمان لازم برای اتمام کارها است. به علاوه خیلی از فاکتورهای موثر هم کاملا از کنترل ما خارج هستند. بیزینسمنها سعی میکنند برنامهشان را منعطف تنظیم کرده و بخشهایی که کنترلی رویشان ندارند را درست مدیریت کنند. این افراد با شکست برنامهریزیهایشان ناامید نمیشوند و سعی میکنند با آزمون و خطاهای فراوان، زمان تقریبی هر کاری را پیشبینی کنند.
آنهایی که عاشق کاغذ و خودکار هستند، برنامهریزی دستی را اجرا میکنند. اما جالب است بدانید که ۹۰ درصد بیزینسمنهای موفق، از تقویمهای آنلاین به خصوص Google Calendar استفاده میکنند. چنین ابزارهایی هم قابلیت یادآوری دارند و هم سایر فاکتورها (مانند بخشهای غیرقابل کنترل و افراد دخیل در پروسه) را وارد ماجرا میکنند. مثلا میتوانید اسم و ایمیل شخصی را که با اون جلسه دارید در تقویم گوگل وارد کنید تا برای او هم یک یادآوری ارسال شود.
تست التراسونیک
تست التراسونیک جهت کنترل ترک های داخل مخزن به کار می رود.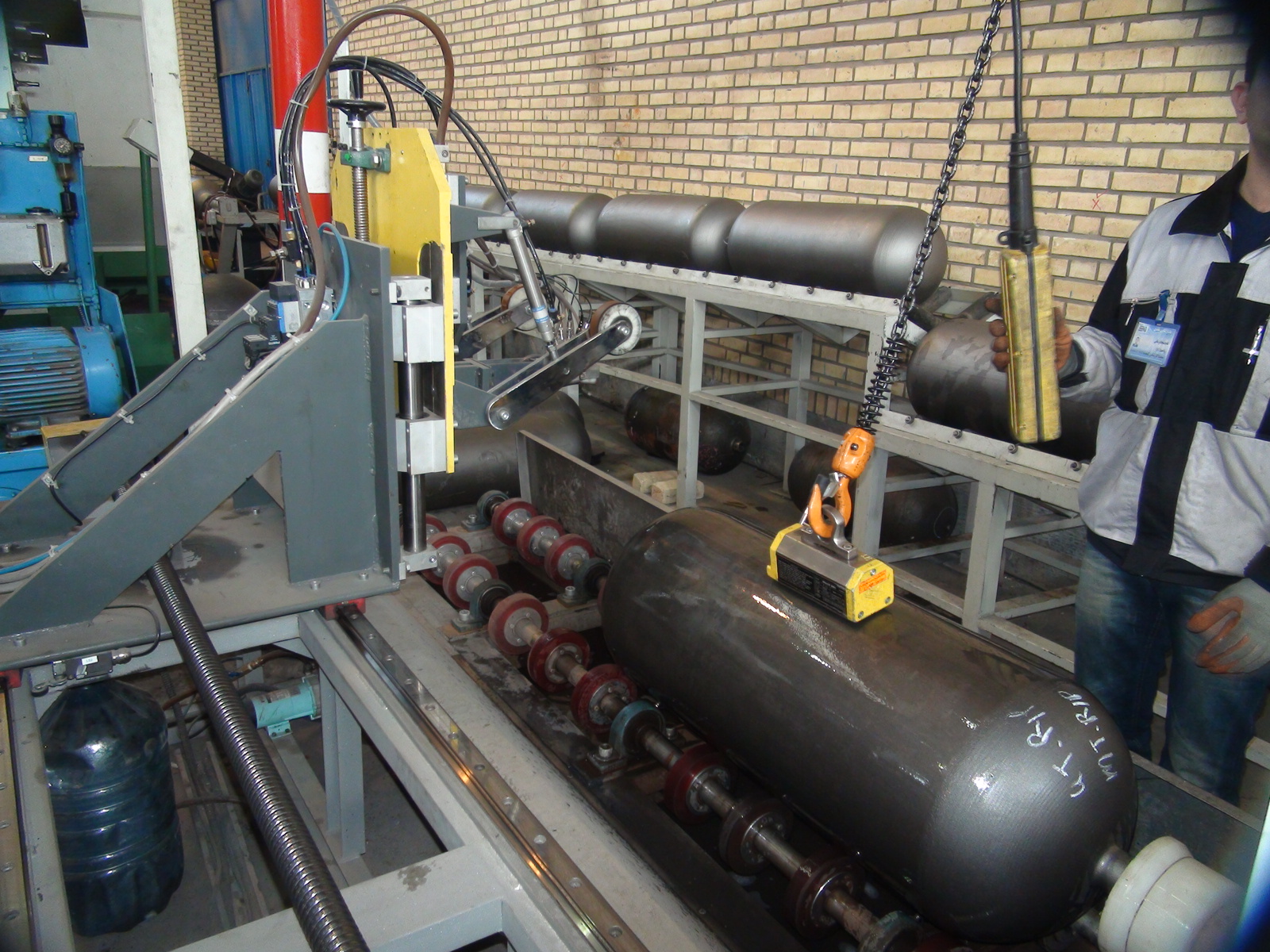
عملکرد این تست بر اساس ارسال امواج صوتی توسط پراب UT و دریافت امواج منعکس شده از عیوب داخلی مخزن توسط ترانسدیوسر می باشد که این عیوب بر روی نمایشگر دستگاه به صورت پیک نشان داده می شود.
روش انجام تست التراسونیک مخازن CNG به صورت غوطه وری می باشد.
تست مغناطیس
تست ذرات مغناطیس (MT) ، یک روش بازرسی غیر مخرب جهت عیب یابی ناپیوستگی های سطحی و زیر سطحی مخازن CNG می باشد.
روش انجام تست بدین صورت است که ابتدا مخزن توسط دو عدد یوک متقاطع ، مغناطیس گردیده و پس از پاشش محلول فلورسنت ، تمامی سطوح مخزن در اتاق تاریک و زیر اشعه ماوراء بنفش (UV) ، بازرسی می گردد.
خط رنگ الکترواستاتیک
هدف از انجام این فرایند ایجاد پوششی مناسب با رنگ الکترواستاتیک جهت مخازن CNG می باشد.
این خط شامل قسمت های ذیل می باشد که به صورت تمام اتوماتیک عمل می کند :
سیستم انتقال :
این قسمت از ابتدا تا انتها ی فرایند توسط کانوایر های هوایی انجام می گیرد . بدین صورت که اپراتور ، مخزن ها را توسط قلاب و جرثقیل باربر روی کانوایر قرار می دهد.
کابین پاشش رنگ :
در داخل کابین رنگ ، 6 عدد گان جهت پاشش رنگ روی مخازن موجود می باشد که کلید تنظیم هر یک از گانها روی تابلو کنترل تعبیه شده است. بعد از اینکه تنظیمات گانها کنترل شد ، کانوایر روشن شده تا مخازن به کابین پاشش رنگ وارد شوند و عملیات پاشش رنگ الکترواستاتیک روی مخازن توسط گانهای پاشش رنگ انجام می گیرد.
کوره پخت رنگ :
این کوره شامل 2 عدد مخزن می باشد که باید قبل از هر کاری هیتر مشعل ها را روشن کرده تا دمای کوره به 200 درجه سانتیگراد برسد و جهت پخت رنگ آماده گردد. زمان مورد نیاز جهت عملیات پخت رنگ 26 دقیقه می باشد.
تونل خنک کننده :
این تونل بعد از قسمت کوره قرار گرفته و دارای 6 عدد فن خنک کننده می باشد که جهت خنک کردن و تثبیت رنگ مخازن استفاده می شود و کلیه مخازن از این تونل عبور می کنند.
سیستم بازیافت رنگ :
این دستگاه با مکش هوای درون کابین پاشش ، فشار هوای داخل کابین را کاهش داده که در نتیجه مانع از خروج رنگ از داخل کابین می گردد. همچنین هوای همراه رنگ پودری از سایکلون گذشته و رنگ های قابل مصرف از غبار هوا جدا می شوند و در مخزن انتهای سایکلون جمع می شوند.
دستیابی به فرمول مناسب جهت تولید رنگ مخازن CNG
در تاریخ 22/06/89 با افتتاح واحد آزمایشگاه شیمی ماشین سازی عابدی ، تحقیقات بر روی رنگ مورد نیاز برای پوشش مخازن CNG مطابق با استاندارد ECE R110 آغاز گردید. با انجام بررسی های انجام گرفته روی نمونه رنگهای تولید شده در کارخانه های رنگ سازی داخل کشور ، مشخص شد که هیچ یک از آنها قادر به ساخت رنگ مطابق با استاندارد ECE R110 نیستند. لذا متخصصین رنگ آزمایشگاه شیمی ماشین سازی عابدی ، مطالعات خود را جهت رفع نقایص موجود در فرمولاسیون رنگ شروع کردند که ماحصل مطالعات انجام شده باعث دستیابی به فرمول مناسب جهت تولید رنگ مخزن CNG مطابق با استاندارد ECE R110 برای اولین بار درایران شد .
در حال حاضر رنگ مصرفی مورد استفاده در شرکت ماشین سازی عابدی نسبت به تمام مواد شیمیایی، فرایندهای مکانیکی ، فیزیکی و خوردگی مقاوم بوده واستفاده از این رنگ باعث افزایش طول عمر مخزن می شود.
کیفیت رنگ مصرفی در کارخانه ماشین سازی عابدی به شرح ذیل می باشد :
Values | Standard | Test Condition | Characteristics |
200C@10 | — | — | Curing Condition |
Ok | ASTM D3359 | Cross Cut Tape Test | Adhesion |
Ok | ASTM D522 | 12.7 mm , Mandrel , -20°c | Flexibility |
Ok | ASTM D2794 | Min 18j | Direct Impact |
Ok | ASTM D2794 | Min 18j | Reverse Impat |
Ok | — | 0-60 | Particle Size |
Ok | — | R-6011 | Color |
Ok | ASTM D523 | 60 Glass , Meter | Glass |
Ok | ASTM D1308 | 30%H₂SO₄ , 100hrs | Acid Resistance |
Ok | ASTM B117 | 5%Nacl , 500hrs | Corrosion |
Ok | ASTM D1308 | Brake Fluide | Polyalkalene Glycol |
دستگاه بسته بندی
بعد از خروج مخازن از خط رنگ ، به منظور جلوگیری از عوامل آسیب رسان و تسهیل در حمل و نقل و انبارش نیاز است که مخازن CNG در بسته بندی مناسب قرار گیرند.
در قسمت بسته بندی ،
مخازن روی پالت های چوبی یا پلاستیکی 9 تایی به صورت 3 ردیف 3 تایی بارگذاری می شوند. جهت جلوگیری از برخورد و حرکت مخازن ، بین هر ردیف ، از دو زیر سری چوبی و بین هر دو مخزن از نایلون های حباب دار یا توری پلاستیکی استفاده می شود.
جهت جلوگیری از زنگ زدگی ، داخل مخزن با پوشش روغنی پوشانده می شود. به منظور ممانعت از ورود گرد و غبار ، رطوبت و اشیاء خارجی به درون مخازن و محافظت از گلویی ، از درپوش شیر و کپ ، روی گلویی استفاده می شود. سپس مخازن بر روی پالت با چهار حلقه تسمه پلاستیکی ثابت می شوند.
جهت محافظت بهتر مخازن از ضربات احتمالی هنگام بارگیری ، حمل و نقل ، گرد و غبار و رطوبت ، پالت مخازن به وسیله چند لایه فیلم استرچ پوشانده می شود.
در نهایت بعد از اتمام مراحل بسته بندی ، پالت ها برای بارگیری به انبار منتقل می شوند.
آزمایشگاه شیمی
در آزمایشگاه شیمی کلیه فرایند های شیمیایی ساخت مخزن از مرحله مواد اولیه ، حین تولید و محصول نهایی از جمله رنگ ، فسفاته و کوئنچینگ تحت کنترل می باشد.
آزمایشگاه شیمی گروه صنعتی عابدی شامل تجهیزات ذیل می باشد:
دستگاه آب مقطر گیری:
این دستگاه جهت تبدیل آب معمولی به آب مقطر به کار می رود . آب مقطر به دست آمده در قسمت دستگاه سالت اسپری و خود آزمایشگاه شیمی جهت تست های آزمایشگاهی و دستگاههای Spining استفاده می شود.
دستگاه ضخامت سنج:
این دستگاه جهت اندازه گیری ضخامت رنگ روی مخازن ، که باید در حالت استاندارد بین 80-60 میکرون باشد ، استفاده می شود.هود:
ترازوی دیجیتال جهت توزین موادی با دقت 0.1 میلی گرم جهت محلول سازی انجام میشود.
هیتر:
جهت گرم کردن محلول شیمیایی ساخته شده و همچنین جهت سریع تر حل شدن و یکنواخت شدن محلول شیمیایی به کار می رود.
آزمایشگاه شیمی جهت رنگ مخازن ، شامل تجهیزات ذیل می باشد:
1. دستگاه سالت اسپری :
مقاومت رنگ در برابر خوردگی را اندازه گیری می کند.
این دستگاه در آزمایشگاه شیمی قرار دارد که برای اندازه گیری مقاومت خوردگی پوشش رنگ مورد استفاده قرار می گیرد. به عبارت دیگر مقاومت رنگ در برابر فرسایش ناشی از مه نمکی توسط این دستگاه مورد ارزیابی قرار می گیرد.
روش کار دستگاه به این صورت می باشد :
ابتدا نمونه رنگ پودری الکترواستاتیک را روی یک پلیت به ابعاد 15*10 به ضخامت استاندارد 8/0 میلی متر می پاشیم. سپس در سطح ورق رنگ شده یک خراش به شکل x ایجاد کرده و پلیت را با زاویه 45 درجه داخل دستگاه قرار می دهیم. جهت انجام تست سالت اسپری ، دمای کابین پاشش ، PH کابین و غلظت محلول نمک بسیار حائز اهمیت می باشد.
در هنگام انجام تست هر 100 ساعت یکبار، قطعه رنگ آمیزی شده را از داخل دستگاه خارج کرده و محل خراش را کنترل می کنیم تا فاقد هر گونه خوردگی و بلند شدگی رنگ از سطح زیرآیند باشد.
2. دستگاه تست ضربه رنگ :
مقاومت رنگ را در برابر ضربه اندازه گیری می کند.
این دستگاه در آزمایشگاه شیمی قرار دارد که مقاومت رنگ را در برابر ضربه اندازه گیری می کند.
دستگاه مورد نظر از یک قسمت محل قرار گرفتن پلیت ، راهنمای لوله ، رها کننده وزنه ، سوراخ کن 9/15 میلی متری و وزنه 2 کیوگرمی تشکیل شده است.
روش کار دستگاه به این صورت می باشد :
ابتدا پلیت رنگ آمیزی شده را در جایگاه مخصوص پلیت قرار داده ، بافشردن دکمه رها کننده وزنه ،وزنه از ارتفاع یک متری رها شده و در سطح پلیت فرود می آید. سپس نمونه پلیت را از زیر دستگاه خارج کرده و محل ضرب دیده را مورد بررسی قرار می دهیم که هیچ گونه ترکی در محل ضربه ایجاد نشده باشد.
3. دستگاه خمش رنگ :
مقاومت رنگ را در برابر خمیدگی رنگ اندازه گیری می کند.
این دستگاه در آزمایشگاه شیمی قرار دارد که مقاومت رنگ را در برابر خمیدگی رنگ اندازه گیری می کند.
دستگاه مورد نظر از دو پیچ گیره ،اهرم فشار و یک خط کش تشکیل شده است که پیچ ها ، نمونه پلیت مورد آزمایش را نگه می دارند و اهرم فشار سبب انحنای پلیت شده و خط کش ، ضخامت خمیدگی محل ترک رنگ را مشخص می کند.
روش کار دستگاه به این صورت می باشد :
ابتدا پلیت رنگ آمیزی شده را در محل گیره قرار داده و پیچ ها را سفت کرده و اهرم فشار را در جهت عکس عقربه های ساعت با زاویه 180 درجه به سرعت حرکت می دهیم تا پلیت مورد آزمایش خم شود. سپس محل خمیدگی را روی خط کش قرار داده تا ضخامت ترک احتمالی ایجاد شده مشخص گردد.
4. دستگاه چسبندگی رنگ :
قدرت چسبندگی رنگ را اندازه گیری می کند.
این دستگاه در آزمایشگاه شیمی قرار دارد که قدرت چسبندگی رنگ را اندازه گیری می کند.
دستگاه مورد نظر از یک چاقوی برش ، ذره بین ، چسب مخصوص پلیمری و برس تمیز کننده تشکیل شده است.
روش کار دستگاه به این صورت می باشد :
ابتدا با استفاده از چاقوی برش ساز ، یک برش متقاطع در سطح مخزن رنگ آمیزی شده ایجاد کرده و سطح برش خورده را با استفاده از برس مخصوص تمیز کرده و محل تقاطع خط را با چسب مخصوص می پوشانیم. سپس چسب را با سرعت و زاویه 180 درجه از سطح پلیت جدا کرده و محل تقاطع خطوط را با ذره بین مشاهده می کنیم تا هیچگونه کندگی و جداشدگی رنگ از سطح زیرآیند اتفاق نیافتاده باشد.
5. دستگاه PH متر :
PH محلول های شیمیایی را اندازه گیری می کند.
این دستگاه در آزمایشگاه شیمی قرار دارد که PH محلول های شیمیایی را اندازه گیری می کند.
دستگاه مورد نظر از یک الکترود تشکیل شده است.
روش کار دستگاه به این صورت می باشد :
ابتدا درپوش الکترود را باز کرده و سطح الکترود را با آب مقطر شسته و الکترود را داخل بافر استاندارد PH7 قرار می دهیم تا دستگاه کالیبره شود. بعد از کالیبره کردن دستگاه ، الکترود را مجددا با آب مقطر می شوییم. سپس ظرف حاوی نمونه را زیر الکترود قرار داده و الکترود را داخل محلول مورد آزمایش فرو برده به طوری که محلول تا بالای دیافراگم قرار گیرد. پس از اینکه نمایشگر ثابت شد عدد نشان داده شده توسط دستگاه را قرائت می کنیم.
6. دستگاه Oven :
مقاومت حرارتی پوشش رنگ را اندازه گیری می کند.
این دستگاه در آزمایشگاه شیمی قرار دارد که مقاومت حرارتی پوشش رنگ را اندازه گیری می کند.
این دستگاه از یک هیتر با ظرفیت دمایی 200 درجه سانتیگراد و یک تایمر تشکیل شده که جهت مقاومت پوشش رنگ در برابر حرارت استفاده می شود.
روش کار دستگاه به این صورت می باشد :
ابتدا دمای دستگاه را روی 180 درجه سانتیگراد و زمان تایمر را روی 30 دقیقه تنظیم کرده و پلیت های رنگ آمیزی شده را داخل دستگاه قرار داده و دکمه استارت را می زنیم. سپس پلیت را از دستگاه خارج کرده و میزان نرمی نمونه رنگ را کنترل می کنیم تا رنگ ، نرم نشده باشد.
آزمایشگاه شیمی جهت فسفاته کردن مخازن ، شامل تجهیزات تیتراسیون می باشد که غلظت مواد شیمیایی درون وان های فسفاته را اندازه گیری می کند.
آزمایشگاه شیمی جهت کنترل فرایند کوئنچینگ ، غلظت مواد شیمیایی درون دستگاه کوئنچ را اندازه گیری می کند. مایع درون دستگاه کوئنچ بافر و جاذب اکسیژن است و جهت خنک کردن مخازن استفاده می شود.
آزمایشگاه مکانیک
آزمایشگاه مکانیک شامل تجهیزات ذیل می باشد :
- دستگاه تست ضربه :
اندازه گیری میزان انرژی جذب شده جهت شکسته شدن نمونه در دمای 50- درجه سانتیگراد که طبق استاندارد و از عرض بریده شده است.
این دستگاه در آزمایشگاه مکانیک قرار دارد که برای اندازه گیری میزان انرژی جذب شده هنگام شکست نمونه مورد استفاده قرار می گیرد.
روش کار دستگاه به این صورت می باشد :
ابتدا نمونه ای از مخزنی که عملیات حرارتی روی آن صورت گرفته ، جدا می شود و پاندول ضربه زننده با قرار گرفتن در زاویه 145 درجه آماده ضربه زدن قرار می گیرد. این تست در ابعاد و دمای استاندارد 50- درجه سانتیگراد انجام میشود. سپس با توجه به زاویه بازگشت پاندول ضربه زننده ، میزان انرژی جذب شده با استفاده از جداول مربوطه برحسب ژول مشخص می شود.
با تقسیم عدد ژول بدست آمده به عدد سطح مقطع نمونه ، میزان استحکام به ضربه نمونه برحسب ژول بر سانتی متر مربع به دست می آید. عدد به دست آمده با الزامات استاندارد ECE R110 مطابقت داده شده و نتیجه نهایی به واحد کنترل کیفیت اعلام می شود.
دستگاه تست کشش :
کشش نمونه هایی که طبق استاندارد و از طول بریده شده اند (ماده اولیه و محصول نهایی) تا زمانیکه نمونه پاره شود که سه آیتم اندازه گیری می شود.
– تنش تسلیم
– استحکام کششی
– ازدیاد طول
سه آیتم اندازه گیری مذکور با استاندارد ECE R110 مطابقت داده می شود.
این دستگاه در آزمایشگاه مکانیک قرار دارد که برای تست کشش ، فشار و خمش نمونه بریده شده از مخزن مورد استفاده قرار می گیرد.
روش کار این دستگاه به این صورت می باشد :
ابتدا نمونه ای از مخزنی که عملیات حرارتی روی آن صورت گرفته ، طبق شرایط و ابعاد و راستای مندرج در استاندارد ECE R110 ، جدا می شود.
با نصب اکستنسیومتر بر روی نمونه و قرار دادن نمونه بین فک های دستگاه و وارد کردن پارامتر های نمونه در نرم افزار دستگاه ، تست کشش شروع شده و نمونه تحت کشش قرار داده می شود . و پس از مدت زمان مشخص ، نمونه گلویی می شود و سپس گسیخته می شود.
نرم افزار دستگاه ، تنش تسلیم ، استحکام کششی و درصد ازدیاد طول را محاسبه کرده و بر روی صفحه مانیتور دستگاه نمایش می دهد. و بعد از مقایسه پارامتر های اعلام شده با الزامات استاندارد ECE R110 ، گزارش به واحد کنترل کیفیت اعلام می شود.
- دستگاه تست خمش:
این تست هم توسط دستگاه کشش انجام می شود و در نهایت نمونه ای که طبق استاندارد بریده شده توسط میکروسکوپ مشاهده می شود تا ترک نداشته باشد.
این دستگاه در آزمایشگاه مکانیک قرار دارد که توسط دستگاه کشش انجام می شود و در نهایت نمونه ای که طبق استاندارد بریده شده توسط میکروسکوپ مشاهده می شود تا ترک نداشته باشد.
- دستگاه پورتابل سختی سنجی :
جهت سختی سنجی نمونه ها استفاده می شود و قادر است سختی را در واحد های پرینل ، راکول سی ، Hlk و غیره اندازه گیری کند.
این دستگاه در آزمایشگاه مکانیک قرار دارد که برای اندازه گیری سختی نمونه های بزرگ و سنگین که جابجایی و انتقال آنها مشکل می باشد مورد استفاده قرار می گیرد.
دستگاه مورد نظر دارای 3 نوع پراب می باشد و جهت سختی سنجی قطعات فولادی و ریختگی دارای تخلخل و همچنین قطعاتی که به صورت سطحی سخت شده اند کاربرد دارد. و توانایی نمایش سختی در واحد های مختلف (HB,HRC,…) را دارا می باشد.
روش کار دستگاه به این صورت است:
هر سه پراب به ترتیب روی قطعه قرار داده می شود و با زدن دکمه روی پراب ، عدد سختی بر روی دستگاه قابل مشاهده می باشد.
تست خستگی
هدف از انجام تست خستگی مخازن ، تعیین مقاومت مخزن در برابر فشار سیکلیک می باشد.
بدین صورت که مخازن در دمای محیط تحت فشار سیکلی متناوب داخلی بین 20 الی 260 بار قرار گرفته و در این شرایط مخازن نباید قبل از رسیدن به تعداد سیکل 15000 (که معادل عمر مفید مخزن است) دچار نشتی و یا پارگی گردند.
تست گلوله
براي انجام اين آزمون بايد مخزني كه توسط گاز فشرده تا فشار 1±20 مگاپاسكال پرشده است را مورد اصابت يك گلوله جنگي به قطر حداقل 62/7 ميليمتر قرار داد.
اين گلوله بايد بطور كامل حداقل از يك سمت ديواره مخزن نفوذ نمايد.
در مورد مخازن نوع CNG-2 ، CNG-3 و CNG-4 ، زاويه اصابت گلوله بايد تقريباً 45 درجه باشد.
نتيجه آزمون زماني قابل قبول است كه :
الف ـ مخزن دچار شكست ترد نگردد.
ب ـ برداشت يا همان كاهش جرم مخزن توسط گلوله بيشتر از 45 گرم نباشد.
يادآوري ـ اندازه تقريبي و موقعيت دهانه ورود و خروج گلوله بايد ثبت شوند.
تست آتش
در اين آزمون هرگاه مخازن
تكميل شده مجهز به سيستم حفاظت در برابر آتش (شير مخزن، وسائل اطمينان تخليه فشار و / يا عايق حرارتي يكپارچه) تحت شرايط آتشسوزي مشخص شده، مورد آزمون قرار گيرند نبايد دچار تركيدن شوند.
يادآوري ـ در طول انجام اين آزمون ، بعلت اينكه ممكن است مخزن دچار گسيختگي گردد بايد فوق العاده احتياط نمود.
نحوه قرار دادن مخزن در معرض آتش
مخزن را بايد بصورت افقي تحت آزمون قرار داد، بطوريكه كف آن تقريباً 100 ميليمتر بالاتر از منبع آتش قرار داشته باشد. به منظور جلوگيري از برخورد مستقيم شعله با شيرهاي مخزن ،اتصالات و / يا وسائل اطمينان تخليه فشار، بايد از سپر فلزي استفاده نمود. اين سپر فلزي نبايد هيچ گونه تماس مستقيمي با سيستم حفاظت در برابر آتش (وسائل اطمينان تخليه فشار يا شير مخزن) داشته باشد.
در حين انجام آزمون وقوع هرگونه خرابي در شير ، اتصالات يا لولههايي كه بخشي از سيستم درنظر گرفته شده حفاظت در برابر آتش نميباشند باعث بي اعتبار شدن نتيجه آزمون ميگردد.
منبع آتش
براي انجام اين آزمون يك منبع آتش با شعله يكنواخت و طول 65/1 متر بايد بطور مستقيم به سطح مخزن و در سراسر قطر آن برخورد كند.
هر سوختي را ميتوان در منبع آتش استفاده نمود. به شرطي كه اين سوخت به منظور حفظ دماهاي مشخص شده آزمون تا زمان تخليه مخزن، بتواند گرماي يكنواخت و كافي را توليد نمايد.
يادآوري ـ به هنگام انتخاب سوخت،مسئله آلودگي هوا را بايد مدنظر قرار داد.
چيدمان و نحوه ايجاد آتش بايد با جزئيات كافي ثبت شود تا در صورت لزوم بتوان مجدداً همان نرخ گرماي ورودي به مخزن را ايجاد كرد.
در حين انجام آزمون وقوع هرگونه خرابي يا غير يكنواختي در منبع آتش، باعث بي اعتبار شدن نتيجه آزمون ميگردد.
اندازهگيري دما و فشار
بوسيله حداقل سه رشته ترموكوپل كه با فاصله مياني حداكثر 75/0 متر در امتداد كف مخزن نصب ميشونددماي سطح مخزن بايد اندازهگيري و كنترل شود. به منظور جلوگيري از برخورد مستقيم شعله با ترموكوپلها بايد از سپر فلزي استفاده نمود و يا ميتوان ترموكوپلها را در داخل پولكهاي فلزي كه سطح اندازهگيري آنها كمتر از 25 ميليمتر مربع ميباشد قرار داد.
در طول آزمون دماهاي سطح و فشار داخلي مخزن بايد در فواصل زماني 30 ثانيه يا كمتر ثبت شوند.
الزامات كلي آزمون
مخازن بايد بااستفاده از گاز طبيعي فشرده پر شده و بطور افقي در فشارهاي زير تحت آزمون قرار گيرند:
الف ـ فشار كاري
ب ـ 25 درصد فشار كاري
بايد بلافاصله بعد از جرقه زدن ، شعله آتش تشكيل گردد. اين شعله بايد در طولي به اندازه 65/1 متر از طول منبع آتش به سطح مخزن و در سراسر قطر آن برخورد كند.
در طول پنج دقيقه پس از جرقه زدن و آغاز اشتعال سوخت ، حداقل بايد يكي از ترموكوپلها دماي 590 درجه سلسيوس يا بيشتر را نشان دهد. اين حداقل دما ، بايد در طول آزمون حفظ گردد.
مخازن با طول 65/1 متر يا كمتر
براي انجام آزمون ، مركز اين نوع مخزن بايد درست بالاي مركز منبع آتش قرار گيرد.
مخازن با طول بيشتر از 65/1 متر
در صورتيكه مخزن تنها در يك انتها به وسيله اطمينان تخليه فشار مجهز باشد اشتعال بايد از انتهاي ديگر مخزن آغاز شود.
اما اگر مخزن در هردو انتها يا در بيش از يك موقعيت از طول مخزن به وسيله اطمينان تخليه فشار مجهز باشد، در اين صورت مركز منبع آتش بايد درست بين دو وسيله اطمينان تخليه فشاري قرار گيرد كه بيشترين فاصله افقي را نسبت به هم دارند.
اگر مخزن به عايق حرارتي نيز مجهز باشد، آنگاه بايد دو آزمون قرار گرفتن در معرض آتش در فشار سرويس انجام گيرد. بدين صورت كه در يكي از آزمونها منبع آتش بايد درست در مركز طولي مخزن قرار گيرد و در آزمون ديگر اشتعال بايد از يكي از دو انتهاي مخزن آغاز شود.
نتايج قابل قبول آزمون
نتايج آزمون زماني قابل قبول است كه گاز داخل مخزن توسط وسيله اطمينان تخليه فشار تخليه شود.
تست انفجار
هدف از انجام تست انفجار مطابق با استاندارد ECE R110 تعیین مقاومت مخزن در برابر گسیختگی در هنگام قرارگیری تحت فشار هیدرواستاتیک می باشد.
روش انجام تست بدین صورت است که مخزن با آب پر شده و فشار داخل مخزن در داخل یک محفظه ایمنی با نرخ مشخصی افزایش می یابد تا لحظه ای که مخزن گسیخته گردد.
در فشاری که مخزن دچار گسیختگی می شود مطابق با استاندارد ، نباید کمتر از 45MPA ) 450 )بار باشد.